Expertise
Our eight-step approach
At Magnor, we take an eight-step approach to every project, whether we’re called to treat municipal drinking water or industrial process water.
Interpret raw-water data
The first step in properly identifying your water treatment needs is to interpret your raw-water data. Too often, misinterpreting data can lead to the wrong treatment, such as using high levels of chlorine, even though the cause has not been clearly identified. That’s why it is particularly important that you get the right support when interpreting your water analysis data.
Magnor can help you interpret that data to better define your water treatment needs. Over the years, we’ve become experts at interpreting both process-water analysis data for various industrial applications and raw-groundwater analysis data associated with known issues.
We specialize in identifying parameters that are not within acceptable limits based on current drinking water regulations or process requirements. We work both with water treatment train designers and directly with customers to meet their specific needs.
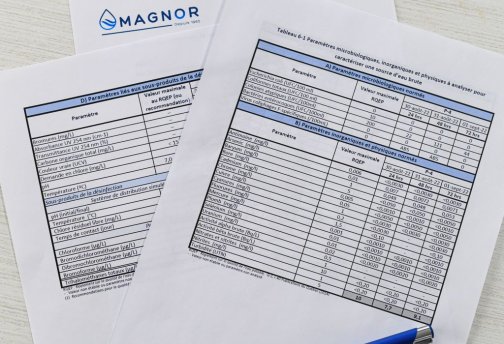
Propose solutions
After interpreting the water analysis data, we help designers and customers determine the water treatment steps to be followed in compliance with regulatory and application-specific requirements.
At Magnor, we use a range of physical and chemical processes to treat various parameters, and we have developed extensive expertise in designing and manufacturing both simple and complex water treatment trains. Our water treatment systems may feature one or more steps that must be connected to deliver a level of water quality that meets government standards or process requirements.
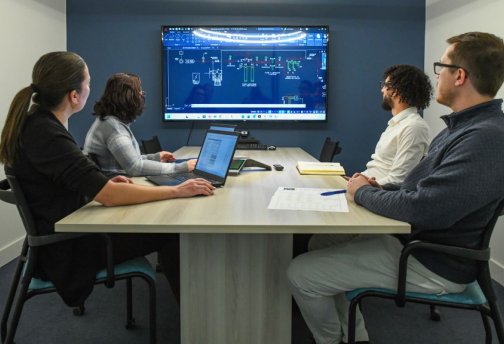
Small-scale treatability tests
We assist customers and their designers in developing and performing treatability tests to address technology uncertainties associated with water treatment projects. Treatability tests are intended to validate treatment solutions for controlled parameters and vary depending on performance requirements outlined in industry-specific standards and regulations. Such tests are sometimes required for a minimum period of time or only as needed to meet complex water treatment challenges.
Treatability tests are carried out on-site by Magnor professionals in partnership with the different parties involved, including municipalities, industries, and designers. Customers are then provided with a report that details our findings and technical recommendations.
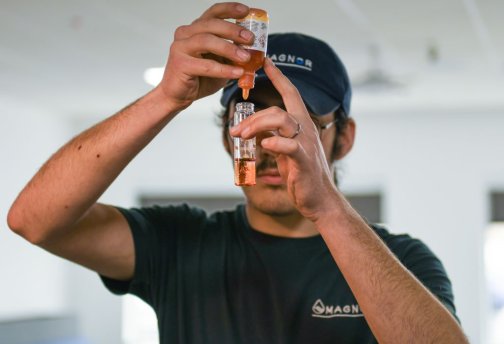
Detailed Design of the chosen solution
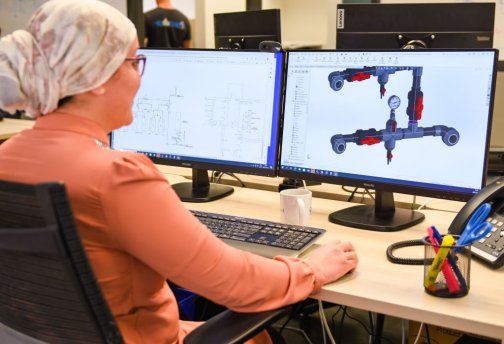
Off-site custom manufacturing
We work with top local vendors to design and build custom water treatment systems at our Boucherville plant. We have a full assembly plant with a lift capacity of 10 tonnes. The advantage of operating our own plant is that we have greater control over the quality of our systems and over timeframes.
Each piece of equipment is assembled and tested at the plant to check that it is working well. That way we can make sure there will be no issues during commissioning. We also perform factory acceptance tests (FAT) when required. Once the equipment has been built and tested, we pack it and ship it to our customers.
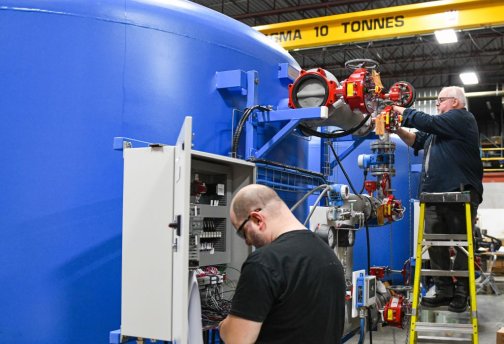
Commission and calibrate the equipment
After the system has been delivered to the customer’s site, a professional contractor will set it up with support from our technical team. Magnor can provide assistance in person or via remote tools depending on the complexity of the project. Once installation is completed, our technicians will commission and calibrate the equipment, adjusting the different settings to meet process requirements.
After the treatment process has been stabilized, our technicians will help customers collect treated-water samples to be sent to a certified lab for analysis. Our technicians will also provide operator training along with instruction and training manuals.
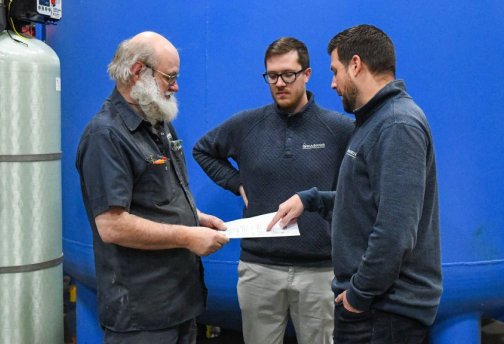
After-sales and preventive maintenance services
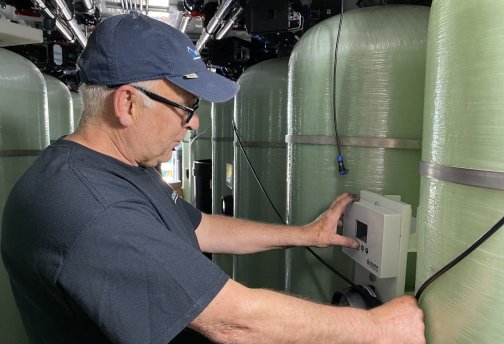
Upgrade the equipment
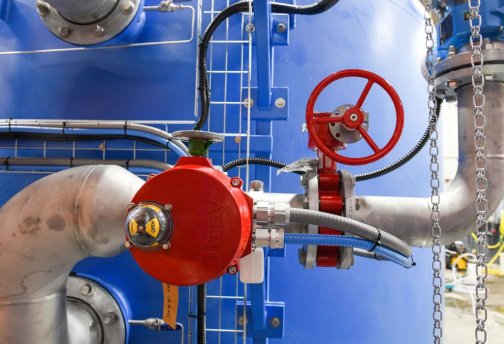